Flex-circuits are a reliable alternative to conventional wiring. By eliminating bulky wires, flex-circuits provide a lighter, more organised and neater appearance while also being capable of forming 3D shapes.
Rigid-flex or flex PCBs are often required to fit into smaller devices. For demanding applications, flexible materials are combined with ultra-HDI technology, offering features as precise as 25 µm and flexible dielectric core also down to 25 µm.
All the commonly used specific materials can be managed by IMP’s manufacturers. We offer a wide variety of high speed/low loss solutions in the microwave boards market, and we are able to provide extremely precise slots, tracks and pads (gap and track +/- 10 µm, accurate routing +/- 50 µm).
Flex-circuits have many advantages:
- Better connection reliability.
- Simplified assembly.
- Improved component appearance.
- Fewer wiring errors during installation and servicing.
- Reduced rework and trouble-shooting time.
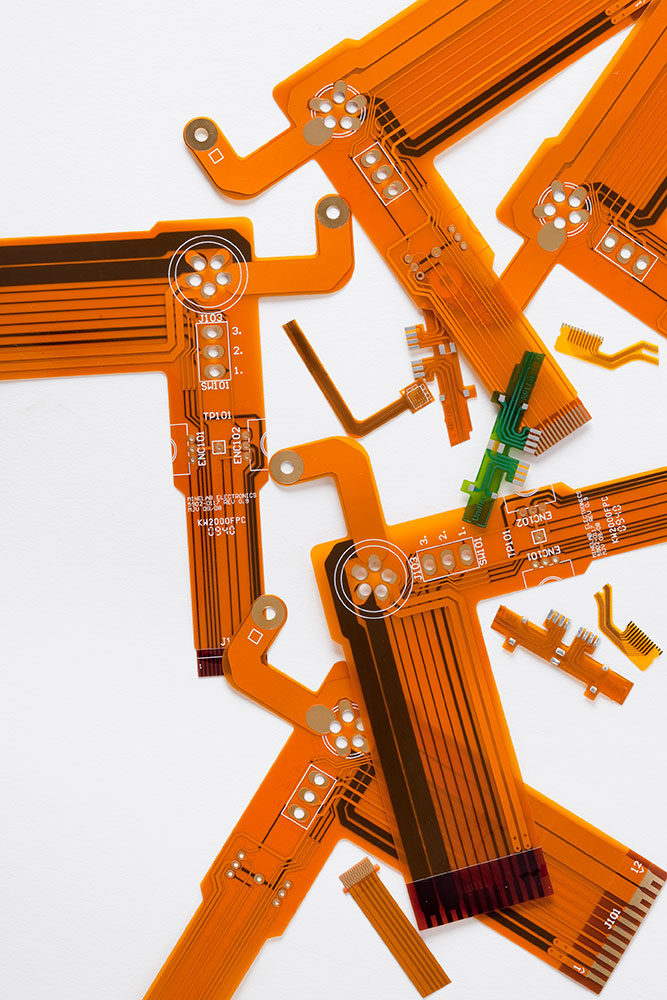
Material Properties Comparisons for FPCs
Substrate Material | Dielectric Constant | Dissipation Factor | Dielectric Strength | Moisture Absorption | Tensile Strength | Elongation |
---|---|---|---|---|---|---|
Polyester | 3.2 | 0.005 | 7000 v/mil | < 0.08% | 25 kpsi | ~120% |
Polyimide | 3.5 | 0.003 | 7000 v/mil | 1.3-3.0% | 25 kpsi | ~60% |
PEN | 2.9 | 0.004 | 7000 v/mil | 1.0% | 30-35 kpsi | ~75% |
Common Substrate Thickness: 25 µm / 50 µm / 75 µm
Cover Material
A thin dielectric material applied to the outside layers of the circuit to insulate the copper conductor. Types available:
Coverlay/Coverfilm
- Combination of film (polyester or polyimide) and adhesive
- Insulated film applied by hot laminating
Cover Coating
- Photo-imageable covercoat (LPI) is produced by a photo controlled process and is used for tight pad spaces
Stiffener
- Used in circuits for applications that require support in areas where connectors or other components are applied
- Used as a carrier panel for automated assembly processing
Capabilities
- Holes size by CNC Drilling: 0.30 mm
- Holes size by punching: 0.50 mm
- Track width / spacing: 150 µm
- Cutting by CNC milling or soft tool with cutting blades: +/- 0.15 mm
- Cutting by hard tool: +/- 0.25 mm (tolerance)
- Tracks location and outline: +/- 0.15 mm
Technical Suggestions
To avoid delamination:
- Increase the pad size without increasing the solder mask opening
- Incorporate tie-downs into the design
Filleting:
- All pads, on both through-hole and surface mount pads, should be filleted to reduce stress points
- This helps eliminate breaking during flexing
Bending:
- Bend radius should be approximately 10 times the material thickness and 1.27 mm away from the plated through hole
- Avoid putting SMD components in the bending area
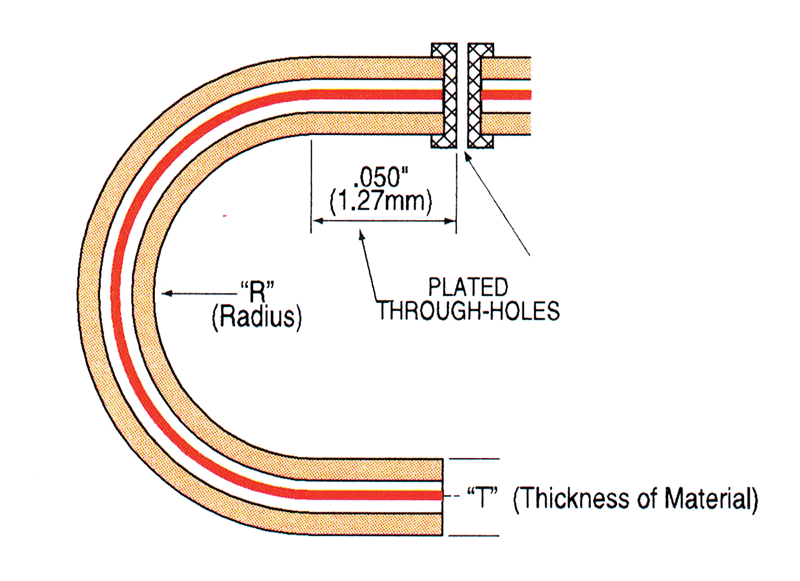
Slots:
- Avoid rectangular holes for small quantities
- Minimum space between board edge and tracks: 0.5 mm
Soldering Considerations
- Since polyimide absorbs moisture, circuits must be bakes (1 hour @ 120°C) before soldering (reference IPC-FA-251 Assembly Guidelines for Single-Sided & Double Sided Flexible Printed Circuits, IPC-TM-650 Test Methods Manual).
- Pads located in large conductor areas; such as ground planes, voltage planes, or heat sinks; should be provided with relief areas. This limits heat dissipation and therefore makes for easier soldering.
Installation Uses Classified as per IPC-6013
- Use A: Capable of withstanding flex during installation
- Use B: Capable of withstanding continuous flexing for the number of cycles as specified in the procurement documentation
- Use C: High temperature environment (over 105°C)
- Use D: UL Recognition
Key IPC Standards for Flex Circuits
- IPC-2223: Sectional design standard for flexible printed boards
- IPC 4202: Flexible base dielectrics for use in flexible printed circuitry
- IPC-4203: Adhesive coated dielectric films for use as cover sheets for flexible printed circuitry and flexible adhesive bonding films
- IPC-4204: Flexible metal-clad dielectrics for use in fabrication of flexible printed circuitry
- IPC-6013: Qualification and performance specification for flexible printed wiring
- MIL-P-50884: (inactive for new designs), printed wiring, flexible and rigid-flex for electronic printed wiring
- MIL-PRF-31032/3A: Printed wiring board, flexible, single and double layer, with or without plated holes, with or without stiffeners, for soldered part mounting
- MIL-PRF-31032/4A: Printed wiring board, rigid-flex or flexible, multilayer, with plated holes, with or without stiffeners, for soldered part mounting
Technical Suggestions
Type 1
Single-sided flexible PCBs containing one conductive layer, with or without stiffeners
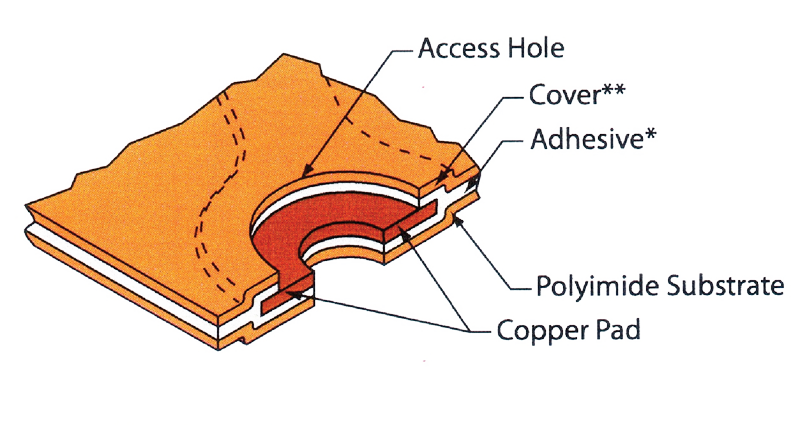
Type 2
Double-sided flexible PCBs containing two conductive layers with PTHs, with or without stiffeners
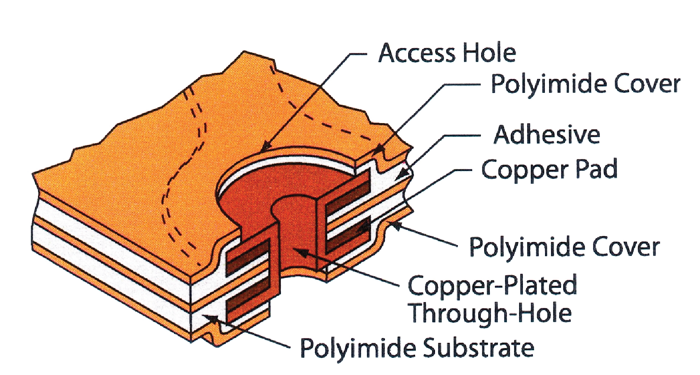
Type 3
Multilayer flexible PCBs containing three or more conductive layers with PTHs, with or without stiffeners
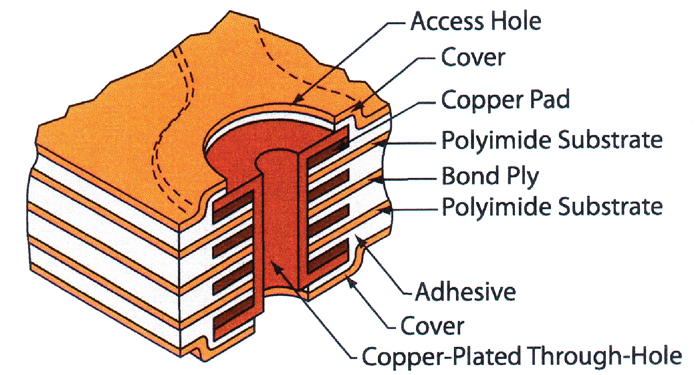
Type 4
Multilayer rigid and flexible material combinations containing three or more conductive layers with PTHs
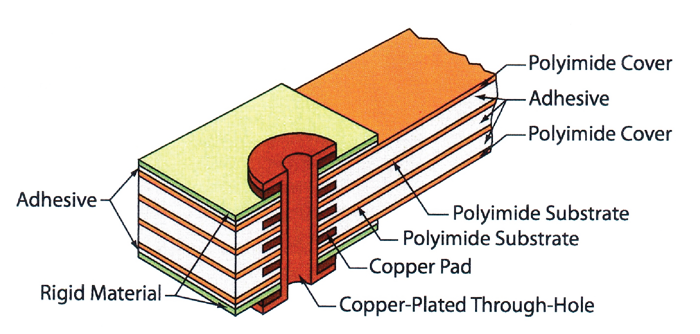
Type 5
Flexible or rigid-flex PCBs containing two or more conductive layers without PTHs
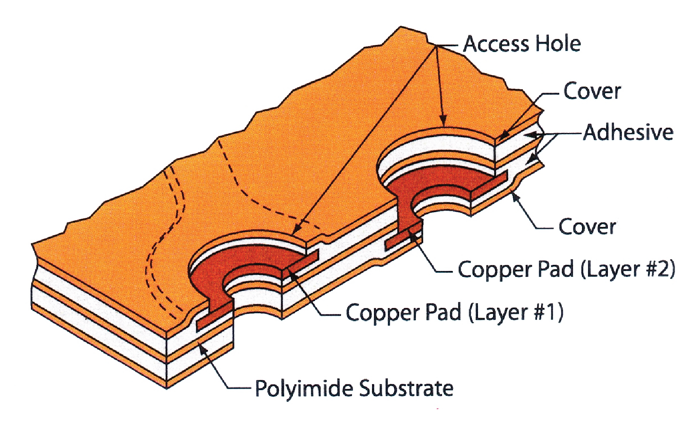